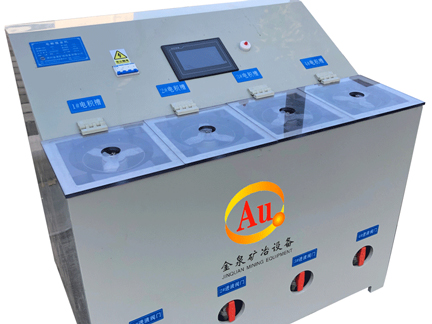
Details of gold recovery equipment
1. Function introduction: The electrolytic gold extraction machine is a technology for wet refining and purification of metals. It can selectively electrolyze valuable metals and is especially suitable for the selective electrolysis (electrolysis) of low-content solutions and solutions with complex components in the metallurgical industry. (accumulation) separation and purification, as well as the recovery of heavy metal ions in wastewater.
2. Technical advantages of gold ecovery equipment:
1)It has the ability to process low-concentration metal solutions, and has higher production efficiency than traditional electrolysis technology to enrich valuable metals in a wider range, from a few tenths of a gram/liter to a few hundred grams/liter of metal concentration for electrolytic production and metal The ability to separate. In particular, it has unparalleled technical advantages in copper-nickel separation and copper-silver separation;
2) It has stronger adaptability to pollutants in the solution and can extract high-purity metals from solutions containing impurities;
3)It has the ability to extract a variety of metals and has the ability to selectively electrolyze metals, and can produce different forms of cathode products (sheets or metal powders) according to the concentration of the solution;
4) The equipment is modular and easy to operate.
-
Innovative Gold and Silver Recovery Extraction TechnologyInnovative Gold and Silver Recovery Extraction Technology
Innovative Gold and Silver Recovery Extraction Technology
Device Utilizes Advanced Electrolysis Methods: Employs rotating cathode, high-frequency pulse technology for intelligent electrorefining without any chemical reagents or consumables, utilizing minimal electricity (350W), with no secondary pollution affecting subsequent treatment of the solution.
Compact Design and User-Friendly Operation: Small, space-saving design allows easy operation without dedicated personnel; incorporates anti-corrosive design to extend component lifespan and handle large processing volumes.
Low Metal Content in Post-Electrolysis Waste: Post-process waste contains less than 2-10 ppm of metal content.
No Special Tools Required for Silver Recovery: Silver content in recovered dross is typically 96-98%, allowing direct refining to produce silver ingots exceeding 99% purity through simple melting.
Single Purification Step for Gold: Requires a single purification step due to gold's small size and tendency to shed, minimizing unnecessary waste.
Series Production and Customization Available: The product is ready for mass production with complete specifications, also offering customization options based on client requirements.
-
desorption electrolysis extraction of goldThe complete system for resin adsorption, desorption electrolysis extraction of gold from micro gold containing waste liquid
The complete system for resin adsorption, desorption electrolysis extraction of gold from micro gold containing waste liquid:
Using specialized gold ion exchange resin, the three-stage adsorption process ensures that the final effluent concentration of gold is below 0.02 ppm, achieving a recovery rate of over 99%.
After the resin becomes saturated, the elution system is activated. After desorption, the resin is washed and reused with eluted solution recirculated to the electrolytic tank for gold recovery.
The eluate is returned to the storage tank for reuse in subsequent operations.
-
99.99% pure silver metalHigh-Efficiency, Environmental-Friendly Silver Refining Equipment Uses Advanced Electrorefining Technology
High-Efficiency, Environmental-Friendly Silver Refining Equipment Uses Advanced Electrorefining Technology
The silver refining equipment employs advanced electrorefining technology. Using 925 silver as the anode and titanium as the cathode, the process operates in electrolytic solution to reduce silver ions at the cathode into 99.99% pure silver metal. This method surpasses traditional nitric acid refining methods in several key aspects:
Reduction of Nitric Acid Use and Discharge: The equipment significantly reduces reliance on and environmental impact from nitric acid, minimizing pollution risks.
Importance of Environmental Protection: For modern industries, where environmental protection is a paramount consideration, this reduction in nitric acid use offers substantial value.
Customization and Flexibility: The device can be tailored to meet production capacity requirements, offering high adaptability. This flexibility not only caters to differing scales of enterprises but also enhances operational efficiency and lowers production costs.
Simplicity and Ease of Use: The equipment is designed for ease of operation, combining the advantages of simplicity and effectiveness in silver refining.
In summary, this equipment excels in terms of environmental protection, customization capabilities, and user-friendliness, making it a highly efficient and sustainable solution for silver refining. Its adoption brings significant commercial value to relevant industries by enhancing resource utilization and operational efficiency while minimizing environmental impact.